How Business Analytics Is Reinventing Warehouse Management Systems
Table of Contents
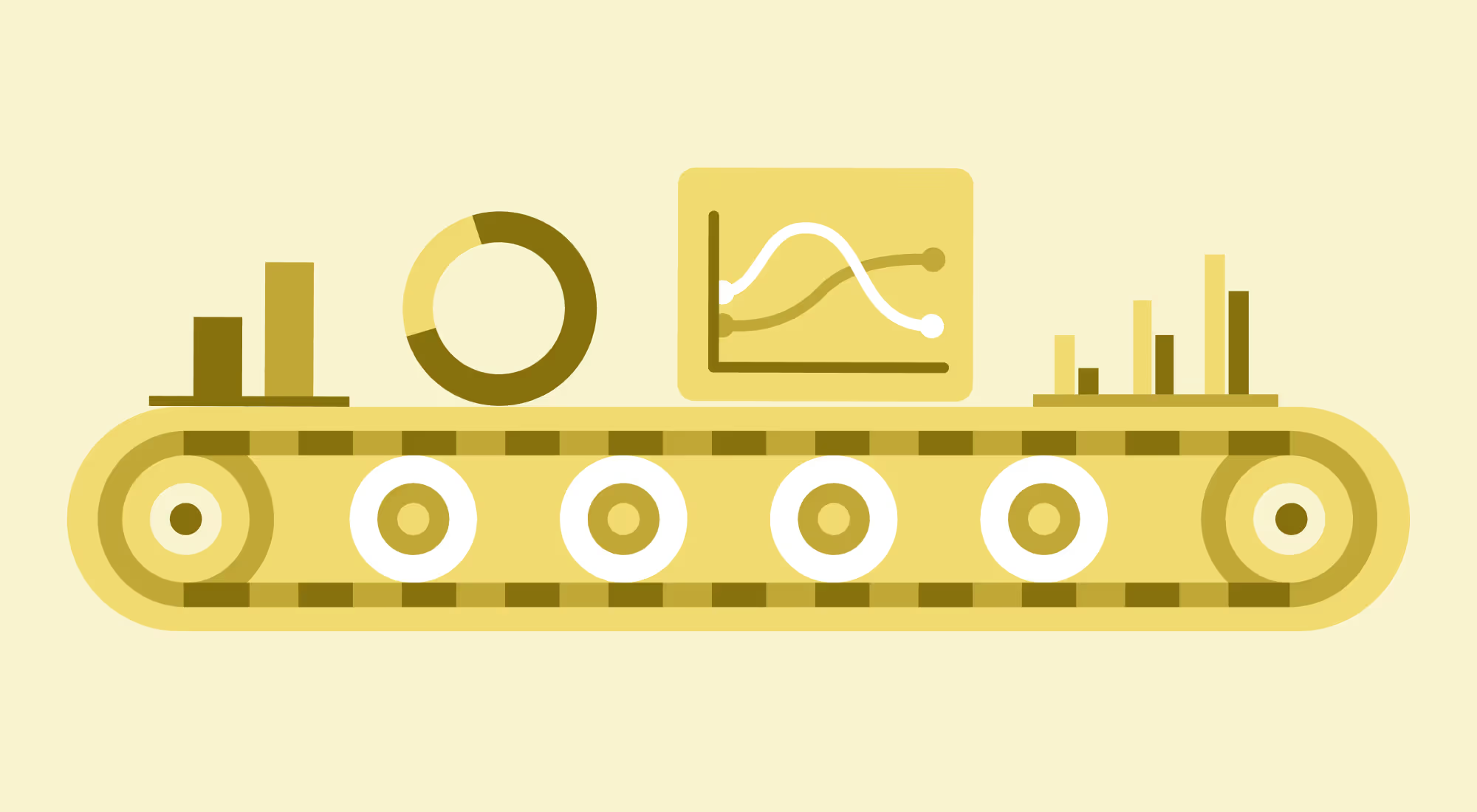
Warehouses have quietly become the most important room in your business. Most businesses still treat their warehouse management system (WMS) like a digital clipboard, a tool for counting boxes and tracking forklifts. Forward-thinking companies are treating WMS data differently. Instead of limiting it to stock counts, they utilize it to forecast customer demand, reduce operating costs, and negotiate favorable terms with suppliers.
Consider this: Warehousing inefficiencies can drain a meaningful portion of operating budgets. Many businesses lose profits to slow processes, disconnected systems, and poor space utilization, often without realizing the impact until margins shrink. That’s lost productivity and millions in missed profit opportunities hiding in your warehouse data.
As global supply chains become increasingly complex and customer expectations become more stringent, the warehouse has evolved from a back-office function into a strategic lever. Yet too many businesses still rely on fragmented or outdated systems that can’t keep up. Let’s explore how business analytics is reinventing warehouse management, helping organizations shift from fighting “fires” to steering smarter, faster decisions across the business.
What is a warehouse management system?
A WMS oversees the storage, movement, and tracking of goods within a warehouse, but referring to it as "inventory tracking" undersells its role. WMS platforms help coordinate the entire lifecycle of a product after it enters the warehouse, from receiving and storing to picking, packing, and shipping to customers.
Modern systems manage inbound receipts, optimize picking paths, automate replenishment to prevent stockouts, and even sync directly with shipping carriers to reduce freight costs. Instead of operating in isolation, today’s WMS platforms integrate with enterprise resource planning (ERP) systems, transportation management systems (TMS), and e-commerce platforms.
A modern WMS connects insights across finance, supply chain planning, and customer service, helping every team make faster, more informed decisions. When fully connected, it transforms from a warehouse tool into an operational nerve center for the business.
Common challenges with warehouse management systems
Even as technology improves, many warehouses still operate in ways that quietly hinder business growth. Warehouse operations generate massive amounts of data, but too often, that information gets trapped instead of being translated into action. Here’s where many businesses stumble and how those challenges quietly ripple across the organization.
Fragmented systems create confusion
One of the biggest problems in warehouse management is data fragmentation. Inventory levels, shipment statuses, and labor productivity are all tracked separately, often updated at different times, and in different formats. When leadership tries to pull the pieces together, they find mismatches everywhere. Which version is correct? How current is the data? Making smart decisions becomes a game of guesswork.
Worse still, when different teams work from disconnected views of the warehouse, their plans inevitably collide.
Poor visibility delays action
Gaps in visibility slow down the entire business. When stockouts, fulfillment delays, or workforce shortages go unnoticed until they trigger missed shipments or rising costs, it's already too late to act without pain. Every delay ripples into lost revenue, higher customer churn, and strained vendor relationships. Problems that could have been addressed early often remain hidden until they become expensive enough to appear on the balance sheet.
Slow reporting kills momentum
Even in companies that diligently track warehouse data, reporting often moves too slowly to be useful. Data is exported manually, cleaned up by analysts, and packaged into dashboards that arrive days or weeks after the fact.
By the time leadership sees a fulfillment trend slipping or an inventory bottleneck forming, the damage is already baked into quarterly results, and the cost is lost time and agility.
Siloed warehouse data isolates problems
When warehouse insights stay bottled up inside operations teams, other departments operate blind. Sales push products that the warehouse can't deliver, finance sets targets based on incomplete inventory values, and supply chain planners build forecasts on shaky ground. The warehouse continues to fight fires that no one else even knows are burning, until the flames spread far enough to affect everyone.
Warehouse teams often find themselves caught in reactive cycles, spending their days putting out fires when a better system could have prevented the problems from arising in the first place. It’s a mindset problem that drains money, time, and customer trust from businesses that can't afford to waste any of it. These challenges aren't permanent. They demonstrate that it's time to stop treating warehouse data as an afterthought and start utilizing it as a foundation for informed business decisions.
The evolution of warehouse management: From logistics tool to business asset
Early warehouse management systems focused on a single goal: tracking inventory. They logged where products were stored and triggered basic replenishment alerts when stock levels dropped. The shift to cloud technology, IoT sensors, and integrated platforms changed that. Warehouses now have real-time visibility into inventory movements, labor productivity, shipment delays, and order accuracy. Data once trapped in paper forms and isolated systems flows across the business in near real-time.
Today’s WMS platforms inform sales forecasts, shape margin strategies, and power smarter supply chain planning. Businesses that treat WMS as a source of strategic insight, not just inventory control, are moving faster and adapting more easily than their competitors.
How business analytics brings warehouse management systems into sharper focus
Warehouse systems collect more data than ever before. Yet without a strong business analytics strategy, much of that information stays hidden in reports that go unread or spreadsheets no one fully trusts. Analytics turns raw warehouse activity into business intelligence.
When WMS data integrates with sales, finance, and planning systems, leaders gain new visibility across their operations. They spot slow-moving inventory before it erodes margins, identify fulfillment risks early enough to protect customer satisfaction, and recognize which warehouses strengthen profitability versus those that quietly drain it.
Industry research consistently shows that businesses that link warehouse data to broader analytics strategies experience improvements in inventory turnover, forecasting accuracy, and fulfillment reliability. More accurate inventory planning, smarter labor allocation, and proactive order management begin to occur when WMS data extends beyond operations and becomes an integral part of business strategy.
Modern platforms like Sigma make this level of insight more accessible by allowing users to explore live warehouse data without deep SQL knowledge. When those closest to operations can spot issues directly, decision cycles speed up and problems shrink before they spread.
Metrics and KPIs that reveal business performance through your WMS
Tracking warehouse activity tells you much more than how efficiently goods move from shelf to truck. When you focus on the right performance signals, you uncover how inventory, labor, and fulfillment decisions shape financial outcomes, customer loyalty, and business agility.
Here are the metrics that matter most and why.
Inventory turnover shows how fast your business moves
Inventory turnover measures the frequency at which stock is sold and replaced within a specified time period. A sluggish turnover rate typically indicates that excess inventory is tying up working capital or that slow-moving products are consuming warehouse space.
Tracking turnover helps finance, sales, and warehouse teams align more closely around actual market demand, rather than relying solely on projections. Low turnover ties up money and creates ripple effects through warehousing costs, storage expansions, and markdown-driven margin erosion. Improving turnover is often one of the simplest ways to boost cash flow and operational flexibility at the same time.
Order accuracy protects customer loyalty
Order picking accuracy shows the percentage of customer orders fulfilled correctly the first time. Even small mistakes add hidden costs: return shipping, customer service escalations, and damaged brand reputation. High order accuracy means fewer avoidable expenses and stronger repeat business from satisfied customers.
Fulfillment cycle time reflects operational agility
Fulfillment cycle time captures how long it takes from receiving an order to shipping it out the door. Shorter cycle times result in faster revenue realization, lower inventory holding costs, and improved customer satisfaction scores.
Long cycle times, on the other hand, often reveal bottlenecks in picking, packing, or inventory availability that need immediate attention. In competitive markets, the ability to ship quickly and predictably can directly influence customer retention and future revenue growth.
Labor productivity reveals hidden efficiency gaps
Labor productivity metrics evaluate how effectively warehouse teams move goods while minimizing excessive labor costs. Moving faster only solves part of the problem. Real efficiency stems from matching workers to the right tasks, reducing overtime, and maintaining high throughput without driving burnout.
Analyzing shifts, task zones, and output together often reveals operational fixes hiding in plain sight. Smart labor optimization strategies often surface unexpected wins. Simple changes, like adjusting picking zones based on employee experience or workload balancing across shifts, can dramatically increase throughput without adding headcount.
Stockout rates signal deeper planning issues
A rising stockout rate frustrates customers and exposes weaknesses in sales forecasting, supplier performance, or inventory replenishment models. Monitoring stockouts closely helps businesses identify planning breakdowns early, before they erode revenue and customer trust.
Warehouse space utilization ties directly to profitability
How effectively you use physical warehouse space impacts the bottom line more than many leaders realize. Poor space utilization inflates storage costs, increases labor inefficiencies, and drives up time-to-ship metrics. Maximizing space efficiency enables businesses to scale their volume without requiring immediate, expensive warehouse expansions. Space optimization does more than pack more products into a building. It streamlines operational flow, improves worker safety, and reduces unnecessary travel within the warehouse. Together, these improvements lead to faster order cycles and lower fulfillment costs.
Each of these metrics, when viewed in context, tells a story that extends beyond warehouse walls. They speak to customer loyalty, financial stability, and organizational resilience.
Preparing your warehouse management system for the future of analytics
Building a smarter WMS starts with building better connections. Cloud-based data warehouses, such as Snowflake and BigQuery, enable the integration of WMS data alongside finance, marketing, and customer service datasets, without overwhelming legacy systems.
Normalizing metric definitions ensures that everyone talks about inventory turnover or pick accuracy in the same way. Flexible analytics platforms enable live querying, freeing business users from relying on static reports or nightly data refreshes. Future-focused businesses develop warehouse data strategies that can scale with them. They design warehouse data strategies that can handle more SKUs, new regions, and shifting fulfillment models long before the pressure builds.
Future-proofing your warehouse operations
Winning warehouses aren’t getting bigger, they're getting smarter. The businesses that rethink space, data, and workflows today will be the ones shaping the market tomorrow.
Companies that rethink their WMS with analytics aren’t chasing minor gains. They’re building faster supply chains, stronger financial performance, and better resilience across every part of the business. They’re making faster, smarter moves across finance, sales, supply chain, and customer service. They’re using warehouse insights to renegotiate shipping contracts, design more effective replenishment models, and identify customer demand trends before their competitors even notice them.
Warehouse data is a front-end competitive advantage. The question isn't whether you can afford to modernize your warehouse analytics. It’s whether you can afford not to.
Warehouse management systems FAQs (frequently asked questions)
What is a warehouse management system used for?
A WMS manages the storage, tracking, and movement of goods within a warehouse, ensuring efficient operations and accurate order fulfillment.
How does a WMS integrate with other business systems?
Most modern WMS platforms connect to ERP, transportation management (TMS), and e-commerce systems, creating end-to-end visibility across fulfillment operations.
What metrics should I track to measure warehouse performance?
Key metrics include inventory turnover, picking accuracy, fulfillment cycle time, labor productivity, stockout rates, shipping reliability, and warehouse space utilization.
What’s the business case for modernizing a WMS with analytics?
Modern analytics turns warehouse operations from a cost center into a source of strategic advantage by improving speed, accuracy, customer satisfaction, and financial agility.